INTRODUCTION
We know how critically important it is to maintain accuracy in results. For that reason, Wonderland Labs takes extraordinary steps to ensure the same accuracy client after client, month after month, year after year.
It can be difficult to understand the steps taken when you’re not there to see them, so I thought I’d share some of those steps with you in this article.
CALIBRATED MACHINES
First, we start with machines built and calibrated by Cal-L in Los Angeles, CA. Former Agilent employees (the company that manufactures the machines we use) are on staff to handle even the most difficult issues. They’re well-respected experts in the industry regarding building, rebuilding, and refurbishing lab equipment, especially Agilent equipment.
REFERENCE SAMPLES
Next, any analytical method to test for alkaloid content must begin with reference samples from a reputable chemical supply house. Our preferred supply house is Sigma-Aldrich. They provide both Mitragynine and 7OH samples with 100% purity. This allows us to calibrate our machines to pinpoint accuracy with precisely measured dilutions made from each original pure sample. We calculate all formulations and dilutions to the thousandth to ensure that any whole number results are as scientifically accurate as possible.
We then build an initial set of reference samples from those pure alkaloids, with 0.001%, 0.01%, 0.1%, 1.0%, 2.0%, 5.0%, 10.0%, 20.0%, 30.0%, 50.0%, 70.0%, 80.0% and 90.0% dilutions. These external reference samples are used twice per year on all our machines to re-calibrate and re-validate our results.
But that calibration is just the beginning.
From those external reference samples, we build a set of internal reference samples that will last us for approximately 6 months of tests. Those reference samples are prepped simultaneously with the external reference samples to ensure the highest possible accuracy. We build a complete set of 1.0%, 1.5%, 2.0%, 5.0%, 10.0%, 30.0%, 50.0%, 70.0%, and 90.0% internal reference samples. Those are pictured above. That set of reference samples then gets sent to a trusted partner lab to validate the accuracy or our internal math.
And this is when the real work begins for maintaining that pinpoint accuracy with our machines. Those reference samples are then used in a very rigorous calibration schedule that happens in multiple stages. The external reference samples are used to build individual calibration curves on each of our machines.
THE MIGHTY CALIBRATION CURVE
Once we crack open our ampule of pure Mitragynine, we then painstakingly pipette out extremely exact dilutions of that reference sample, to build a series of data points to create what’s called a Calibration Curve.
Running multiple tests at each of those dilutions (concentrations) generates a calibration curve. This happens by testing 3 separate preparations of each dilution of the reference material. We then take the average of each of those testing results to build a single data point. Once we get a complete set of numbers, we plot them in a spreadsheet. The ultimate goal is to have a perfectly straight line appear from those data points. Since this is the real world, though, that rarely happens. We can get close to a perfectly straight line, but with so many data points being considered, no matter how perfect our sample prep or our math is – the line will only be nearly a straight line.
Once we’ve built those graphs, we then feed those numbers into each machine individually (we have 3-4 machines dedicated to testing Kratom at any given time). The machine then generates a curve based on those numbers to get an exact percentage from 0.1% all the way up to 100% concentration. If we have been careful enough in our preparations, the machine will be calibrated to 0.01% accuracy. And, our goal is to get each machine we’re testing on, to be within 0.1% of each other. It’s not always a simple task, but it’s important enough that we do our best to achieve that every time we calibrate.
Here is an image of a typical Calibration Curve from 2022:
Full calibration testing is completed every 3 months to verify our calibration curves remain accurate. That testing data is painstakingly logged with all the other paperwork the lab requires.
DAILY / WEEKLY ACCURACY TESTING
But quarterly calibrations aren’t enough for our obsessive-compulsive selves and staff. And this is where the internal set of reference samples we crafted play a critical role. Below is an image from our log book from early in 2023. Each tech is responsible for running this entire series of tests once per week.
Our calibration schedule is as follows:
- Quarterly, we run the full external pure sample from a chemical house.
- Weekly, we run an abbreviated version to verify and validate our results.
- Daily, we run 1-2 random reference samples as an added check and to keep the chemistry flowing in the machines.
- Per Client, we run the internal reference standard we have that most closely matches their “expected” result.
And this is where our OCD really shines: If we get a result that doesn’t match what a client expected, unlike other labs, that triggers a series of protocols to double-check ourselves:
- FIRST, we do an automatic re-prep of the client’s samples.
- SECOND, we prep a reference sample matching the result we got
- THIRD, we take a random previous client’s sample, and run that alongside.
This way, we can be sure that the results we’re seeing weren’t an anomaly, due to bad homogenization, a dead spot in the sample, or whatever else it might be. Nothing is more critical to our lab and our techs than maintaining pinpoint accuracy in every test we complete.
3RD PARTY VALIDATION TESTING
We regularly send out samples to 3-4 external labs that we trust. Two of those labs are popular labs for getting Kratom samples tested (at a much higher price than we test Kratom for). But this gives us further validation that our results are dead on. And, the good news is, that 99% of the time, when we get testing done at external labs, we are either exactly on target with those other labs, or ever so slightly higher.
It’s critical to note the procedure we take for ensuring the accuracy of results that we send out for third party validation:
- We first homogenize the sample in question.
- We then split that sample into 6 equal parts.
- We then test each of those 6 samples.
- Lastly, we send each of those samples out to external labs and wait for the results.
It’s rare that we ever get results back with any more than a 0.1% difference between our results and any trusted external lab that we send our samples to. More often than not, our samples are within just a few hundredths of a percent.
What happens if we get a contentious sample where the client is finding it difficult to believe our results? We send the exact sample(s) we have at our lab out for potency testing at our expense. This is a rare occurence, but maintaining accuracy in our Kratom testing is truly of the utmost importance to us here at Wonderland Labs. And, reputations are easily lost, so we go take extensive measures to know, without any doubt, that the Kratom testing results we provide to any client, are as accurate as scientifically possible.
SPENT BIOMASS TESTING
Once we complete the prepping of a sample, there is the spent biomass that is left over. Theoretically, if our sample prep was accurate and we were to test that spent biomass, the resulting potency should be 0.0%.
Since there isn’t enough spent biomass to do a proper sample prep, we run a sample alongside the one we are currently testing, using the same material. We simply quadruple the amount of material we prep. This way, once all of the chlorophyll and alkaloids are extracted from the material, there will be enough left to run an additional test, using the spent biomass as the material to be tested.
Once the extraction process completes, we remove all of the liquid from that biomass. Once it’s dry, we then do a very quick wash with Methanol, to remove any alkaloids that were extracted but remained behind stuck to the biomass. We then carefully re-dry this material at a low temperature to protect the integrity of the material.
Then, we run another sample prep, as if this were the original unextracted material, to see what we get. With our extraction / sample prep process, we typically remove 99.95% of all alkaloid content minimum, with a more typical result of 99.99% of alkaloids. Knowing this number in advance, we compensate for that tiny (insignifacant trace amount) in the final numbers.
EXPECTATIONS VERSUS REALITY
One of the biggest questions we get, especially when results don’t match expectations, is this:
How can I trust your results?
[INSERT NAME HERE] lab got us results that were higher than your results.
So, they must be right, and you must be wrong.
It’s in our nature as humans to want to believe the things we want to believe more than the things we don’t want to believe. Who doesn’t want their results from their Kratom testing to be at least 1.5% Mitragynine content or more for their raw Kratom powder? And who wouldn’t want their results to be 1.8%, 1.9%, or even 2.0%?
I get it. We want to believe in results that match our expectations and discard results that don’t. But, after nearly 20 years of testing virtually all of the Kratom on the market, we have built up detailed portfolios of strains, varieties, and locales of Kratom.
And one secret I’ll let you in on is this: There likely aren’t nearly the number of varieties and strains that we have all been led to believe there is. Many are blends, or simply different names for the same variety of Kratom to attract more buyers and to have something unique to bring to the marketplace. And, we have sent samples out to various labs at random times, and can’t count the number of times results came back from those labs higher than we know the samples to be.
But that is not the point of this discussion.
THE BEARER OF BAD NEWS
As a lab, we often have to be the bearer of bad news…often. And we know what the immediate response is going to be. But this is the thing:
Regardless of what results people want or hope to see,
to have integrity as a testing lab,
we must report what the science tells us is true.
In fact, modifying the multipliers on our machines can easily produce inflated results. There is a field in any machine’s testing parameters called a “Multiplier” that allows results to be multiplied by any number necessary to get an accurate result. If the Calibration Curve has been carefully constructed and set up, this is rarely the case, especially when testing 0.1% up to 100% dilutions during setup.
That means if the actual result is 1.2% for a particular Kratom powder sample, but the multiplier is set to 1.25x, the machine will report a result of 1.5% instead of 1.2%. It’s that simple. This effect gets more extreme when working with higher concentration extracts. If the multiplier on the machine is just a 1.06 instead of a 1.00, a 70% strength extract would report as a 70 x 1.06 = 74.2% extract.
Now, that might feel good at first, but a 4.2% inflation over an actual 70% material is quite substantial. If the multiplier was set to 1.25, then the material would report as an 87.5%, which is obviously a mile off. Depending on the workload, depending on individual setups, there are so many factors that come into play when taking a sample from preparation to final result. From the precision measurement when the sample is first prepped, to the amount of solvent blended with that material to make the mobile phase, to every step in-between – it’s an amazing feat when two individual labs report identical results.
For us, the main reason for accuracy isn’t just integrity;
It goes way deeper than that.
How so?
Some of our clients are making thousands, hundreds, or millions of dollars in product decisions based on our testing. If we chose to report a 1.2% raw material as a 1.5%, and a purchase is made from that reported result, it could be devastating all the way down the line:
Customers who purchase this material are connoisseurs today and can usually tell the difference between a true 1.5% powder and a 1.2%. Those who purchase this material as a 1.5% and then make mathematical extraction formulation decisions based on these numbers will be sorely disappointed when they compare their expected results from their actual results. A supplier who purchases a large amount of this powder to sell to a lot of distributors, will inevitably get a lot of backlash when any of those distributors test the material, only to find out that it was actually a 1.2% and not a 1.5% as they had been told. And the list truly does go on.
In another example, if a raw Kratom powder with an average Mitragynine content of 1.5% is off by just 0.3% — that equates to a 20% difference in the result. (1.5% is exactly 20% higher than 1.2%). This gets even more extreme when working with higher concentration extracts. Take a high concentration extract being made from this raw Kratom material, and a 70% expected result would end up only as a 56% result.
Heads could roll with those kinds of discrepancies. And these are just a couple examples of why it’s critical to maintain pinpoint accuracy in testing results, especially regarding raw kratom powders, kratom shots / liquids, and kratom extracts.
This is exacltly why Wonderland Labs goes out of its way
to maintain integrity and accuracy in its results.
THE BOTTOM LINE / MY PERSONAL HISTORY
I’ve been in the Kratom industry for nearly 20 years now. A few years back, I was on the Board of Directors for the Botanical Legal Defense. We won a lot of early victories in states that were looking to ban Kratom or make it a Schedule I drug. When we were first starting, that was all our own money being spent to help protect the growing Kratom community.
That grew into something larger than we ever imagined. We started taking in large donations, and began hiring lobbyists whose costs were in the tens of thousands per piece of legislation.
I went to Springfield, Illinois, with a dear friend and colleague to change a law. We were dressed in our nicest suits, put on our lobbying hats, shook lots of representatives’ hands — and managed to change minds! I was shocked. Illinois had a bill that was going to ban Kratom. David and I managed to shake enough representatives’ hands and provide persuasive enough arguments that the law was changed to make Kratom legal in Illinois for those 18 and older.
That is the moment we realized that we could effect change, that we could make a real difference in the Kratom Community. That was a powerful moment and a powerful feeling. And that is what led me to where I am now with Wonderland Labs.
The Botanical Legal Defense started to take up way too much of my time and energy. It became a very high-energy position that was taking up more of my life than I could give. More change was needed in more states, and the Botanical Legal Defense became a full-time job. I had too many responsibilities to continue to devote that much time to the cause. So, I had to bow out.
So, I left.
But my intense desire to make a positive difference in the Kratom community
and to fight for this plant I believed deeply in never left me.
I thought that if I opened my testing lab to the public, but at a fraction of the price that other labs were charging for Kava and Kratom testing, that this could be my way to continue to give back to the community. It wasn’t on the scale of the Botanical Legal Defense, but it was a way to stay connected.
I believe deeply that part of legitimizing Kratom, was to follow all the rules that the FDA had set out for the manufacture of products intended for consumption. If we, as an industry could show that we were doing everything we could to be compliant, by testing Kratom products that were manufactured under cGMP conditions, that we, as an industry would have to be taken more seriously than we may have been taken otherwise.
What I could do was make testing affordable to the smaller manufacturers, to the start-ups, to the people who believed that they could make a go of responsibly offering Kratom for sale.
I hired the best method developers I could find, to help us build SOP’s specifically for Kava testing and Kratom testing. We then began to specialize in both Kava and Kratom testing, building up a portfolio of varieties and species from as many sources as possible.
I love being in the lab. I love sharing and discussing results with clients, and I realized that my passion for the Kratom and the Kava community could still have a positive impact.
And, to this day, despite so many accusations and attacks on our lab, despite those who have chosen to falsify our certificates, and despite us making mistakes along the way as we struggled to keep up with demand, while learning how to handle the difficulties and roadblocks that happen simply by being in the Kratom industry – we are still here, still working to better ourselves, the lab, and our results.
Maintaining accuracy is one of the core ways to build trust with our clients, and it’s a task we take on more seriously than most will ever know. One result can potentially affect so many things down the line, both positively and negatively.
For that reason, maintaining accuracy, by rigorously calibrating our machines, by validating results both internally and externally to maintain pinpoint accuracy is one of our core missions daily.
We sincerely appreciate your trust and loyalty throughout the years. We know that it’s because of that trust that we still exist and are flourishing as a lab today, as we look to the future, and other ways that I can continue to give back to a community I’m deeply passionate about and always will be.
WHY CERTIFICATES OF ANALYSIS?
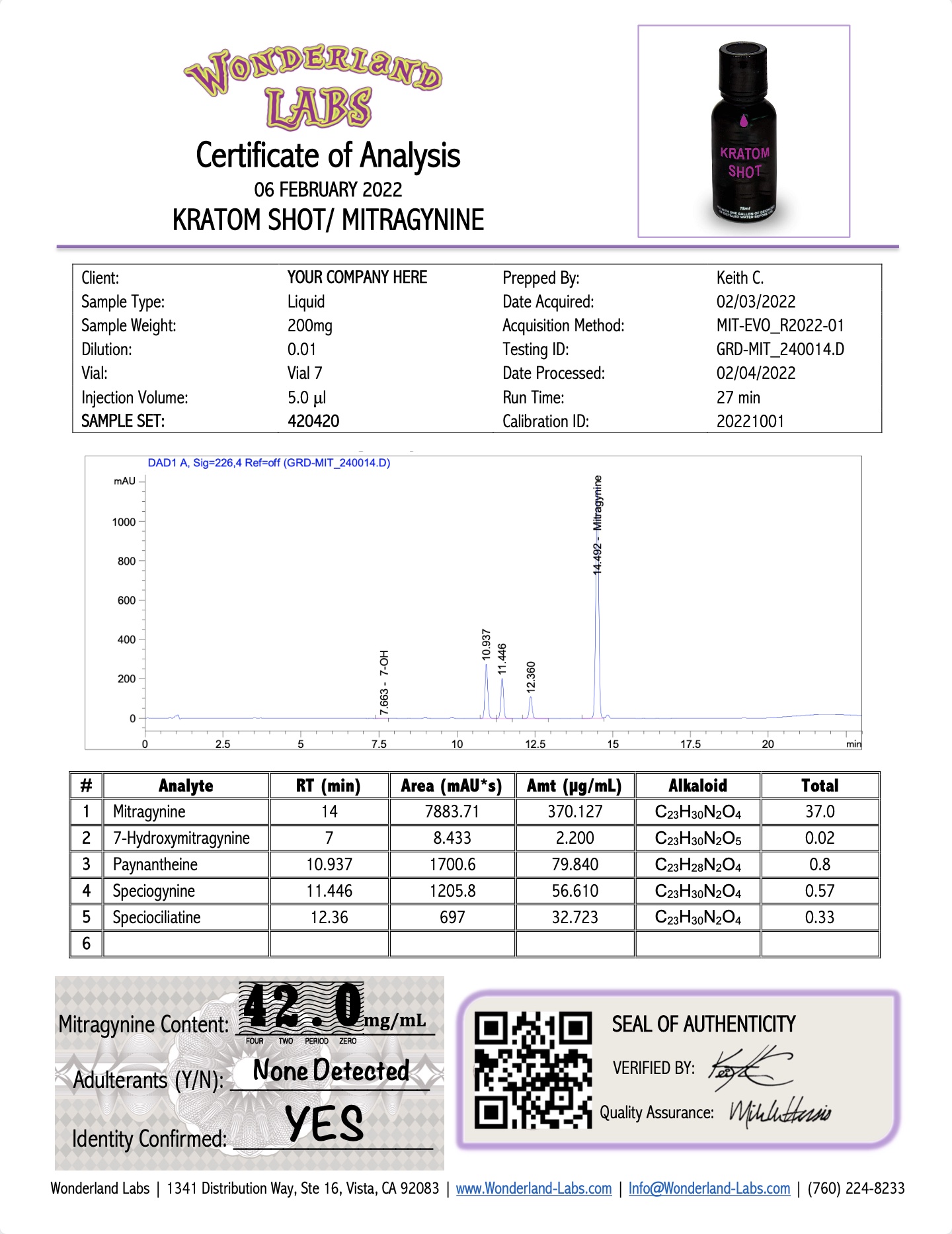
A Certificate of Analysis will confirm that any material is safe for consumption according to FDA guidelines. It doesn’t mean it’s legal for consumption, it just means that if the tested material were to be consumed, it would not contain any of the common pathogens that are most-often and most-likley to be found in foods and/or dietary supplements.
CONTACT US
1341 Distribution Way, Ste 16, Vista, CA 92081
Email: info@wonderland-labs.com
Phone: (800) 647-3154
Call us TOLL FREE
GET A NO-OBLIGATION QUOTE | OUR FAQ’s
OPERATING HOURS: 8-4, Monday – Friday, PT
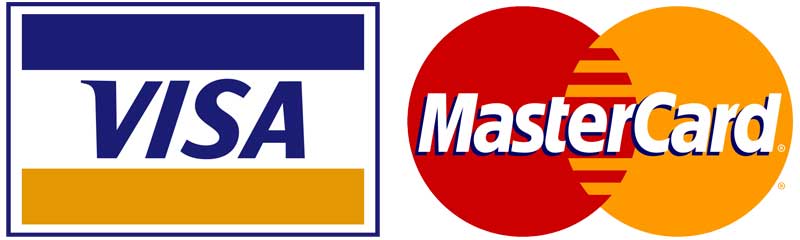